Condacam 3.1 - News
Half a year after launch the new Condacam 3.1 receives a steady positive feedback. Significant new developments in Concacam 3.1 still enable a faster programming and more effective tool paths. Key feature of Condacam 3.1 are the highly modern HSC/HPS strategies and the innovative milling of contact surfaces or the new selection functions.
HSC/HPC-milling with setting of entry points
innovative plunging via slot-ramp, helix, simple ramp as well as the linear entry. Special feature of HPC/HSC- strategies (also called adaptive milling) opposite to the conventional strategies is that the tool load is kept constant over the entire milling process. By this way solid carbide tools with a high level of process reliability can be used and also feeds with high speed. Tool life is significantly extended which means that long lasting milling processes can be implemented with a tool. Furthermore greater steps in the depth can be realised in the Z-axis. The larger plunge step causes an evenly cutting wear over the whole cutter length of the tool whereby all together a greater material removal can be achieved.
Intuitive limitation of machining areas during finishing
Using this function limited machining areas let be defined in a simple innovative manner. The machining is only made as long as the tool is able to keep contact to the selected surfaces. The limitation orientates itself to the contact area between tool and the selected surfaces. Using this technique when finishing flat areas or at contour parallel-, offset-, pencil offset-, circular-, circle spiral-, rectangle-spiral finishing and pencil milling enables the direct and precise machining on and at surfaces.
Completely reworked roughing strategies (including rest material roughing) with soft tool paths by S-Linking, smooth approaching and tool path rounding.
A further innovation within the realm of clearing-planes (offset-, offset/model and pendular roughing) is the better use of free plunging areas in free-milled zones. During adjustment of residual materials for softer tool paths or at the lateral step of over 50% of the tool diameter, this new developed algorithm rounds off this new strategy.
Re-worked finishing strategies Soft tool paths by S-linking, smooth retracting and the tool path rounding is now a part of the strategies offset-finishing, pencil-offset, finishing of flat areas, pocketing, rest material finishing, complete finishing and Z-level finishing (machining between the planes).
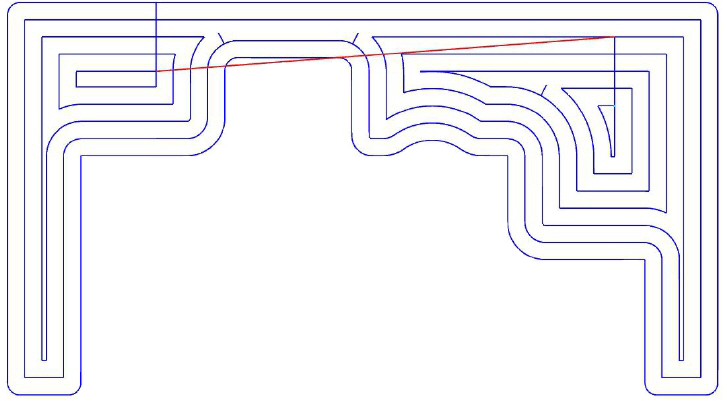
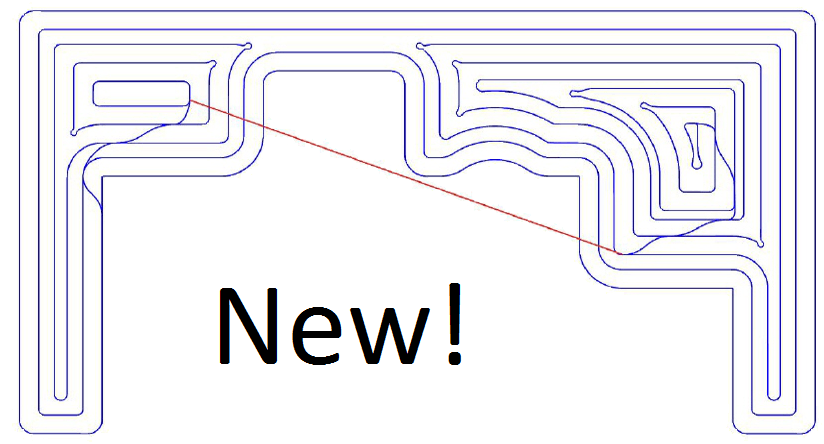
New "finishing between two curves" With a 3D-constant path distance and spiral step.
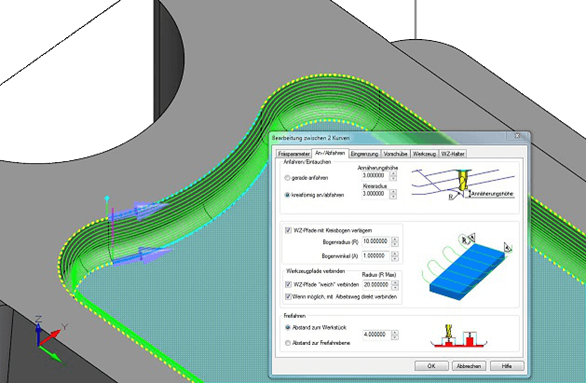
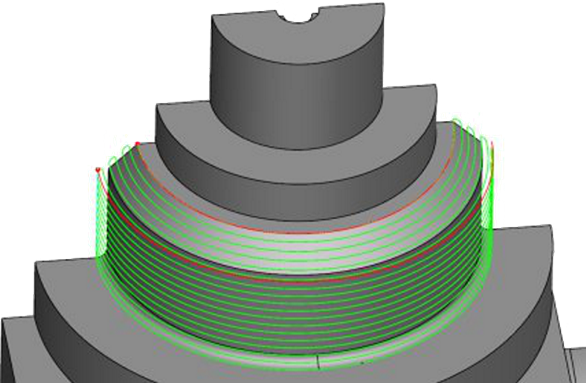
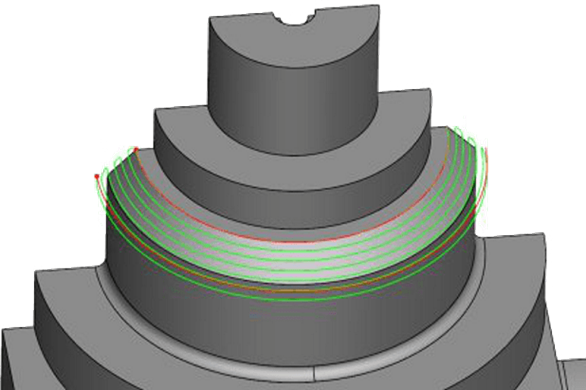
Graphic- and render-technique with temporary contour- and surface-highlighting.
Also new render-technique for object snap symbols and temporary text display (with better display quality).
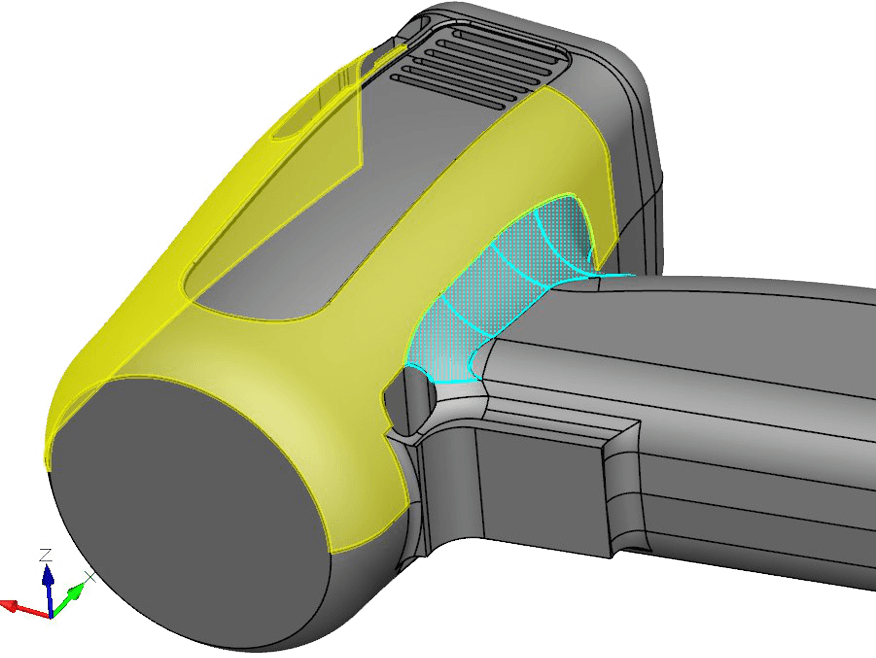
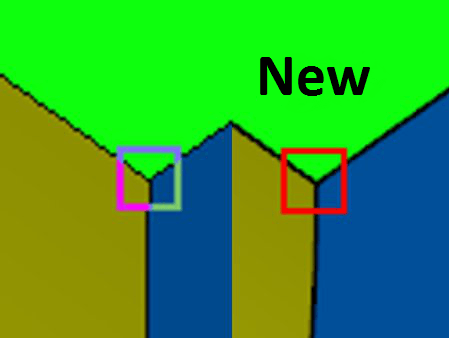
Selection function for contours and contour sections directly on a 3D model. With the contour selection chains of edges will automatically be selected on the 3D model. The selected contours can be used of all 2.5D-strategies (for example pocketing) and for 3D strategies (for example boundary curves).
The new entry- and exit options for thread milling. In the event of small differences between tool diameter and bore diameter the options “centre entry/ exit” and “centre entry/exit with slope” enable a secure entry-/exit. Furthermore these entry-/ exit methods can be more advantageous in the multiple step.
The new selection function "Same-coloured selection” is used for the selection of elements such as lines or faces with the same colour. All visible elements will automatically be added to the selection having the same colour than the selected element. If the string-key is held down during the selection the selection mode reverses. That is, already selected elements with identical colour can thus be removed from the selection.
For the extraction of polylines the new function “extract edges” allows behind the selection of surfaces also the selection of boundary curves directly on the model.
Enhancement of term specification in the report for per-second
output.
New postprocessor simulation-options for the scaling of units. These enable now the CNC-output in other units such as e.g INCH or output formats without comma.
The function measure "radius-circle/ circular arc" allows the measuring of contour radii by selecting of edges directly on the model.
The new strategies “drilling” and “drilling milling” allow now the input of a start depth. This can indicate the drilling position or the start position of the bore in the Z-axis regardless of the selected elements (for example drilling circle).
Furthermore for drilling, thread milling and drilling milling can be selected behind the selection of drilling circles also shell surfaces directly on the model.
The nesting function “nesting contour elements” is complemented with a further option. The de-selecting of the option “part-in-part nesting” enables that contours within a component are not be recorded as internal boundary but nested with the component. Besides that, the internal contours can be open. Labels or other contours, needed for further machining strategies, can additionally be nested.